
#TOWER PRO MICROSERVO PRO#
Let it cool, then re-attach the tube to the servo output shaft with the pin.Tower Pro SG90 Micro Servo Motor is available to buy online in India at Circuit Uncle. With the tubing off the servo, slip the brass rod inside the tubing slightly, then use a small torch to flow solder in the gap between the rod and the tubing (capillary action will draw the solder in). If you wanted a solid axle, shorten the tube (so only a cm or so extends away from the servo), and get a piece of brass rod (hobby store again) that will slip-fit inside the tubing. The tubing can serve as the axle the brad keeps the tubing secured and rotating with the servo output shaft.
#TOWER PRO MICROSERVO INSTALL#
Install a small pin (a small brad nail would work OK) through the hole. Replace the tubing over the output shaft, aligning the holds. Remove the tubing from the shaft, then reassemble the servo with the now drilled gear output shaft. The plastic should be soft enough to make this fairly easy. Using the holes as a guide, drill through the shaft (slowly and carefully - don't rush it). Clean up any burrs from the drilling, and remove the dowel from the tube.įit the tube over the end of the servo gear output shaft. Then - use a small drill (a hobby drill press would be best, but it can be done with a dremel tool and a small drill bit - provided you put the piece in a vice, and hold the drill perfectly vertical) to drill through the tube, dowel, and other side of the tube - the detent you made in step 5.
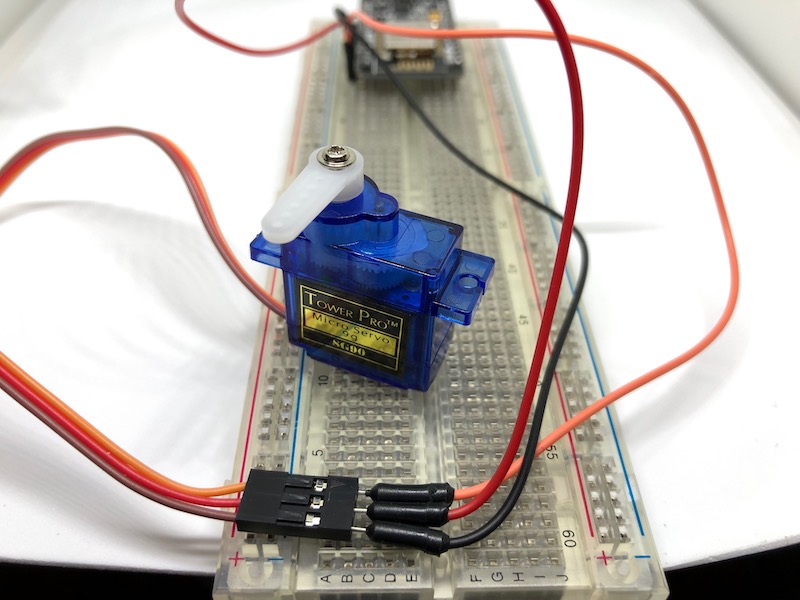
Now - using your mark as a guide, take a small nail and use a hammer to "indent" the mark - don't hammer through it - you're just making a guide detent. Remove the tube, then fit a piece of doweling inside the tube (you can get this at the hobby shop as well) - the dowel should be a snug, but not tight fit.

Cut a piece of the tubing off (using a tubing cutter), as long as you need for your axle.įit the tube over the output shaft on the gear, then make a mark on the tubing about halfway between the end of the shaft and the end of the tubing. Once you have the output shaft gear removed, get a piece of brass tubing slightly larger than the output shaft, from a hobby and crafts store (or similar) a snug fit on the shaft would be best. If it doesn't look like it can be done, then you might need another method. Here's what I'd try to extend the servo shaft:įirst - take the servo apart basically just the top off, then carefully remove the output gear - the design of the servo will influence this step, so be careful. This is my first project and I've been surprised to discover that figuring out the mechanics has been much harder than figuring out the wiring and programming. Sorry for my repeatedly wrong terminology. I've checked data sheets and found nothing. So I'm hoping someone knows what that size is. But to find a standoff/spacer that size, I need to know what that size is. So my thought was that if I could find a spacer/standoff in the size of the screw used to hold the propeller on the horn, then I could use that to attach my wheel (I can make the attachment at the wheel side any size I want). My glue-based attempts left the little propeller attached and glued the propeller to try to get more area to press against. So basically, if that little horn ring where a centimetre deep/long, I'd be golden. The wheel cannot be right up against the servo but needs to be a little distance from it - about a centimetre.
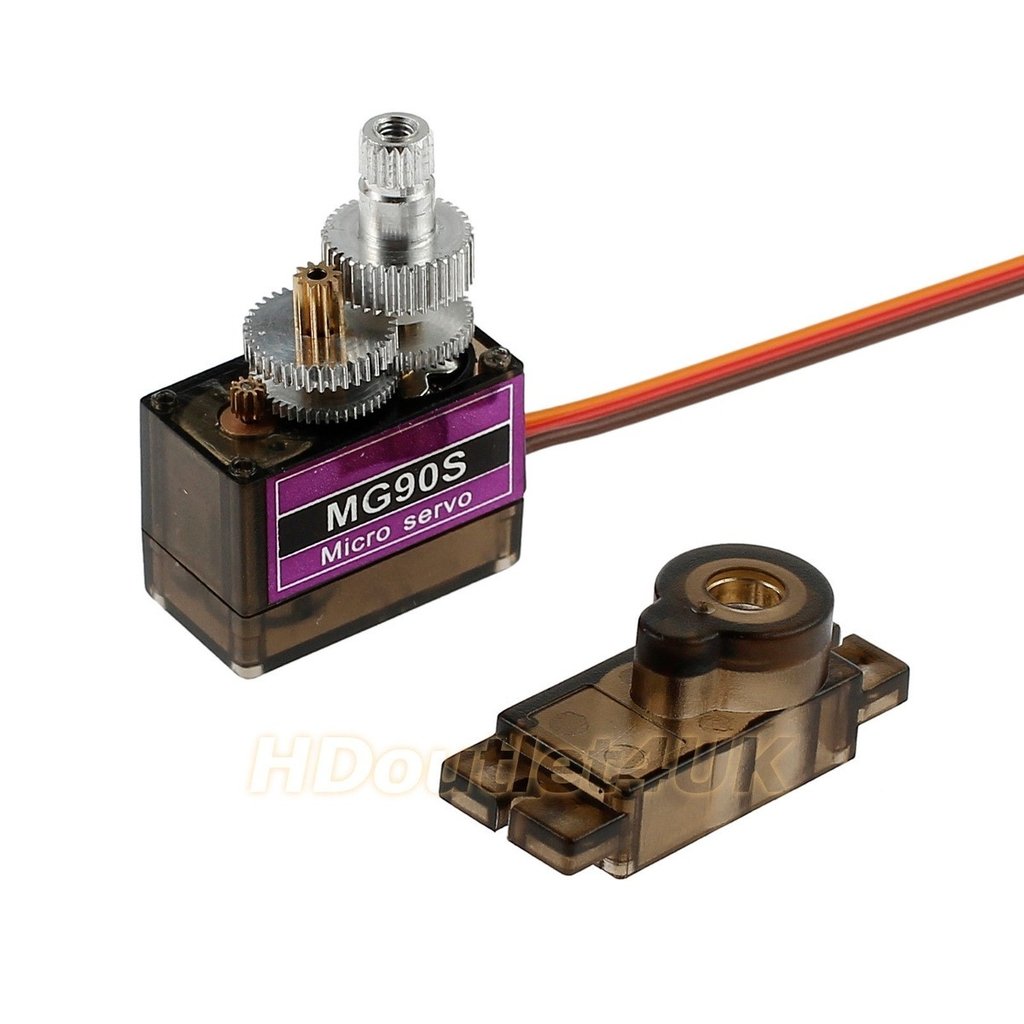
So I have a wheel that I want to turn to a particular angle with the servo. As you've figured out, you'd need some pretty special adhesive to achieve the same torque specifications Using glue as you suggest, only leaves a small ring shaped face for the load to be applied, not as pressure, but as a shear load. Technically, if you're interested, it moves the shear load away from the gap between the two parts to be effectively inside the parts. Have you noticed the little splines on the shaft (little zigzags going around it) ? You'll also note that there is a matching set on the horn, this is to provide a degree of perpendicularity for the forces to be transmitted from the motor to the load. So you mean the plastic/wood (sharper and more course than an equivalent metal thread) screw that screws through the horn and into the motor shaft ? What is the 'front' of a (hobby) servo? Maybe there is an understanding on this, but I'm not aware of it - my intuition says it's not the side with the servo horn on it, that is the top - guess, I could be about to learn something Not quite sure what you mean - by propeller you mean the servo horn? (google)
